If occupants aren’t comfortable, not only will they complain, be less productive, or avoid the space when possible, it will also exacerbate the problem of face coverings. While 75 degrees and 50% relative humidity may be fine for traditional attire, adding a face covering can make it unbearable.
Understanding that we are trying to create a cultural shift of making masks commonplace during this pandemic, we need to do everything we can to make the experience comfortable. The best advice here is to make sure when making operational and ventilation decisions, it would be a best practice to also account for thermal comfort. For instance, if your HVAC system can’t handle more ventilation air without raising humidity levels, maybe another approach is warranted. ASHRAE 55 is a good resource to review for comfort conditions that addresses temperature, humidity and clothing levels. 2 degrees cooler may cost you some energy, but it may also reduce the conflicts on masks.
Increased humidity in a facility can also create other sources of irritants such as mold, mildew and unwanted water on surfaces. At 75 degrees, if your space humidity is 60%, and your dewpoint is around 60 degrees (the temperature when moisture condenses out of the air), any surface in your facility that is 60 degrees or less will start to condense. Toilets, uninsulated water piping, ductwork, even basement walls. At 70% relative humidity, the dewpoint is near 65F. At this point many surfaces start to absorb moisture, such as insulated pipe, drywall that’s either on a below-grade wall or near a cooling supply, ceiling tiles, etc. When any surface that has organic material (paper, dust,etc) reaches 90% relative humidity, it can grow mold. If water is 100% relative humidity, and mold can start at 90% relative humidity, that means these surfaces that are condensing at the above conditions have been able to grow mold for a far greater amount of time. The point of all this is that moisture starts to be an issue long before you see it.
If your facility does not have humidity sensors, and you’d like to see what’s happening, there are several low cost options.
If you would like a very cheap, visual indication, many can be had for less than $4 each. However, I would strongly discourage this approach. These are not very accurate, and sometimes a visual display of a potential issue to non-technical personnel creates more of a headache.
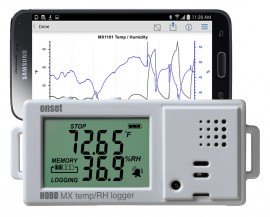
A better approach, and the approach I use as an engineer is a data logger system, such as a HOBO. This device can record, save, and some models can transmit thousands of temperature and humidity points and are discrete, starting at less than $100. This allows the facility operator to collect enough data to make an educated decision on what the operational changes are having on a facility without investing in a very expensive building automation system or upgrade. These have the added benefit of not advertising the fact that you are monitoring space conditions, which reduces questions and more importantly tampering.
The most important take-away from this information is that we need to look at all effects of system operation and modifications, not just a single criteria. Decisions regarding system operation are just a small piece of the equation when considering re-occupancy of a building, but are important nonetheless.
Contributor: Stephen Oskin, PE, LEED AP, Director of Mechanical Engineering at Barton Associates.
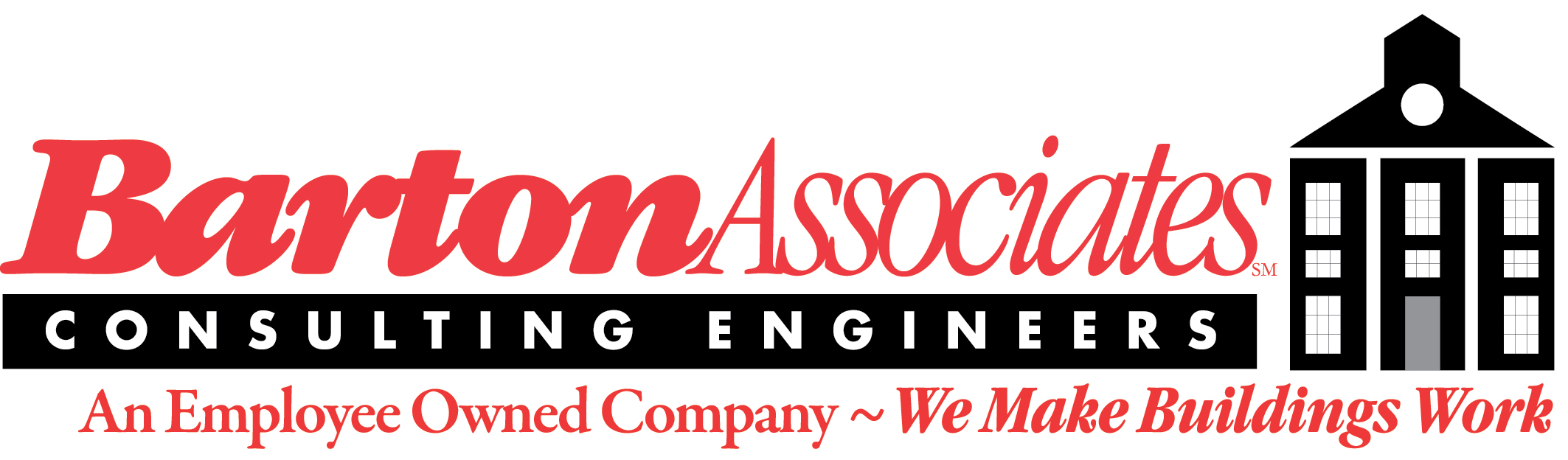